New Book Tells Story of How American Roots Has Succeeded as a Union Manufacturer
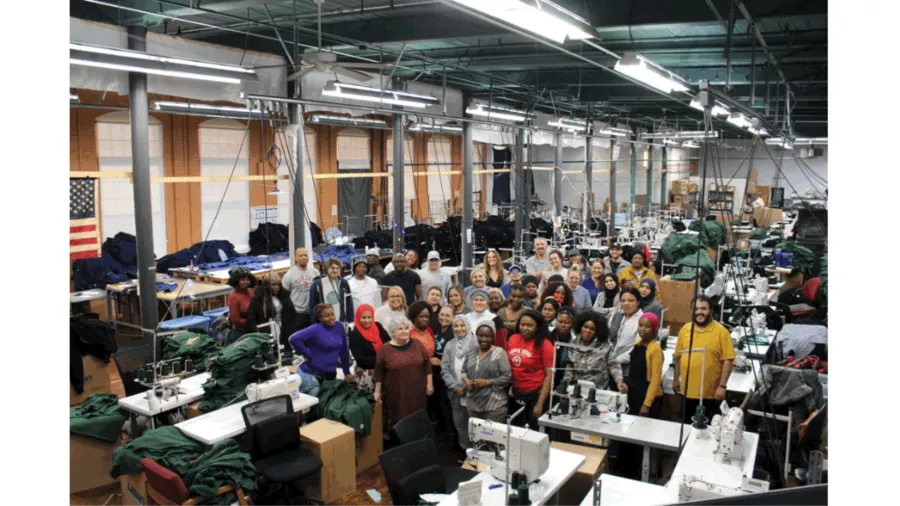
PHOTO: American Roots workers (USW 366) Courtesy of American Roots.
Nine years ago, Portland native and former AFL-CIO organizer Ben Waxman and his wife Whitney brought their dream to establish a clothing manufacturing facility to life. Their founding principals included only using domestically sourced materials and making their products with skilled local union labor. Fast forward to 2024 and Westbrook-based clothing company American Roots has 75 employees, most of whom are members of USW Local 366, with company revenues north of $20 million.
Author Rachel Slade's new book “Making It In America: The Almost Impossible Quest to Manufacture in the U.S.A. (And How It Got That Way)” focuses on the Waxman's company and how they have been able to run it successfully, despite many challenges.. The book has received excellent reviews and made it to #1 on Cosmopolitan magazine’s Best Nonfiction Books in 2024 and the Financial Times Top Business Books to Read in 2024.
During a Maine Voices Live Conversation at Mechanics Hall in Portland last week, Slade and the Waxmans discussed the book, the company's successes and challenges and what must be done to bring back good union manufacturing jobs to the US. Slade said many Americans became more awake to the problem of outsourcing our manufacturing base during the covid pandemic when supply chain problems deprived nurses and first responders of proper personal protective equipment (PPE) and ships from Asia couldn’t be unloaded fast enough.
“That’s when I think that everybody caught up with my sense of alarm, that we couldn’t take care of ourselves and our people anymore because we were no longer manufacturing here,” said Slade.
As Slade noted, President George Washington made building a manufacturing base a major priority after the American Revolution. In the colonial era, England forced the US to become dependent on Great Britain for most of its manufactured goods. In his first address to Congress in 1790 that America in order to be “independent of others for essential … supplies.”
Traditionally Maine has had a strong manufacturing sector producing textiles, shoes, paper, ships and much more. But so-called “free trade” agreements like the North American Free Trade Agreement and China’s entry into the World Trade Organization in 2001 have decimated our manufacturing base, causing the loss of tens of thousands of good union jobs in Maine alone.
Ben Waxman experienced this decline first-hand as his parents’ cape making business closed in 2002. Before returning to Maine, he worked for fifteen years as an organizer with the AFL-CIO visiting places like Bethlehem, Pennsylvania, Youngstown, Ohio, Flint, Michigan and Millinocket in Maine trying to preserve jobs and benefits for manufacturing workers. While visiting a woolen mill in Massachusetts, he stood in the 110 degree heat looking at several looms covered with cobwebs and had an epiphany.
“I looked at Whitney and we had this moment and I said, ‘We’re going to build a fucking factory,’” said Waxman.
He considered building boats and making blankets, but one night when he was out snowplowing with a friend he looked at the label on the fleece vest he was wearing saw the big “Made with USA fabrics” lettering with “Assembled in El Salvador” in smaller letters. He vowed his facility would not only source USA-made materials, but assemble them in the US. He used his union connections to develop a customer base for union apparel. Since then, it has expanded its customer base to many other customers.
“The labor movement built this company and I have no qualms about that. It was building and construction trades unions, it was the industrial unions, public sector unions who said, ‘We’re going to walk the walk, talk the talk and we’re going to buy American and buy union,’” said Waxman. “Private industry has now stepped forward and there are some great companies that are also giving us business.”
Challenges
Running a union textile manufacturing business in this day and age presents enormous challenges. Finding American manufactures to source zippers, grommets and cotton fleece certainly wasn’t easy. But one of the hardest parts has been securing long-term working capital. American Roots has reportedly increased its revenue year by year, up to 40 percent at times, but it still can’t get a line of credit from a bank and has to rely on individual investors.
“This year we’re starting to see that pay off where our company is going off like a rocket ship,” said Ben Waxman. “But cash is still the issue because you can grow, grow, grow, but if you can’t feed the burn, you’re in deep shit. It is very difficult to operate without sustained capital on a regular basis.”
It’s also impossible to compete on price with countries like China, where the average wage for garment workers was just US $217 a month in 2019, according to the International Labor Organization. In 2022, American Roots workers earned on average $47,000 a year, plus benefits, three weeks of paid vacation, holidays and sick days. At the same time, China’s manufacturing industry is heavily subsidized and has been “dumping” products on US markets at artificially low prices below the cost of production.
“There’s this grand vision, especially in Chinese industrial policy to put European and American manufacturers out of business so we are beholden to that country’s productivity,” said Slade. “It’s critical to their survival.”
She said while the price points for American Roots apparel are much more because they are produced more ethically, we should also consider environmental impact of the “fast fashion” industry. According to the UN Environment Programme (UNEP), the textile industry is the second-biggest consumer of water and is responsible for about 10 percent of global carbon emissions — more than all international flights and maritime shipping combined. Meanwhile, the UNEP found that the average consumer bought 60 percent more pieces of clothing in 2019 than 2004 with each item kept only for half as long.
Whitney Waxman said while not everyone may be able to afford their products, it’s important to consider whether it makes economic sense for the average American to buy 68 pieces of cheap fast fashion products in a year, compared to a quality piece of clothing that provides dignified employment and helps a local family send a kid to college or buy a home. Ben Waxman pointed out that these overseas companies typically make a 300-400 percent profit on products that are made in sweatshop conditions for poverty wages and few workplace protections.
Slade also noted that part of the problem is that people who lost jobs in the manufacturing sector and moved into the service economy are making 2/3 on average of what they made before, which is why it's harder to afford products made by other American workers.
"We talk about what can we afford, why can’t we afford these things anymore, [but] part of it is that we have lost economic power when we lost manufacturing… while the very wealthy have gotten exceedingly more wealthy over that same period of time,” said Slade. “So there’s much less distribution of wealth in the United States and that’s part of the reason why these things are so expensive to us.
How to Bring Back US Manufacturing
Ben Waxmanlikes to quote his old boss, the late AFL-CIO President Rich Trumka, who used to say, “The economy is not like the weather. You can predict economic conditions with good policy.” In discussing what policies the US needs to support domestic manufacturing, Slade goes back to the founding of the country when President Washington’s Secretary of Treasury Alexander Hamilton came up with three recommendations. They included tariffs to slow down the importation of cheap goods; banking to ensure that people who wanted to get into industry had access to financing and infrastructure to ensure that the supply chain is robust and strong.
Slade also argues that unions could do more to invest in domestic union manufacturing. She noted that in other countries like Germany union pensions typically invest about 13 percent in local manufacturing. Public employees pensions account for nearly $8 trillion in investments, but they are managed by people focused on bringing in the highest short-term returns. Slade argued that following the lead of Wall Street investors can be “contradictory” when considering that these pensions are “working people’s capital” that could be more invested in working people. Slade said there is a movement afoot to get these pension funds to rethink investment strategy and focus on what will benefit workers, such as the boom clean energy infrastructure construction.
“This is a big moment in America and our fate is being decided,” she said. “It starts today in terms of who is going to making what and where is our energy going to come from and how efficient it is going to be.”